Inside The Coastal Racing Factory GasGas Machines
Photos by Trevor Hunter & Mack Faint
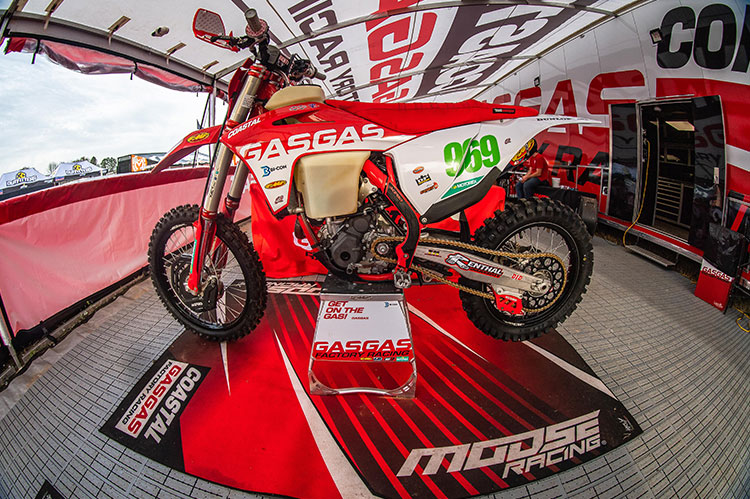
We’ve all dreamed of riding a factory bike since the day we first threw a leg over a bike. Endless titanium, machined components, and one-off parts engineered with a single purpose behind it — to win races. Well, I got a chance to ride a near factory bike, as well as look over a few race winning, championship contending off-road race bikes at the recent Snowshoe GNCC while under the Coastal Racing tent.
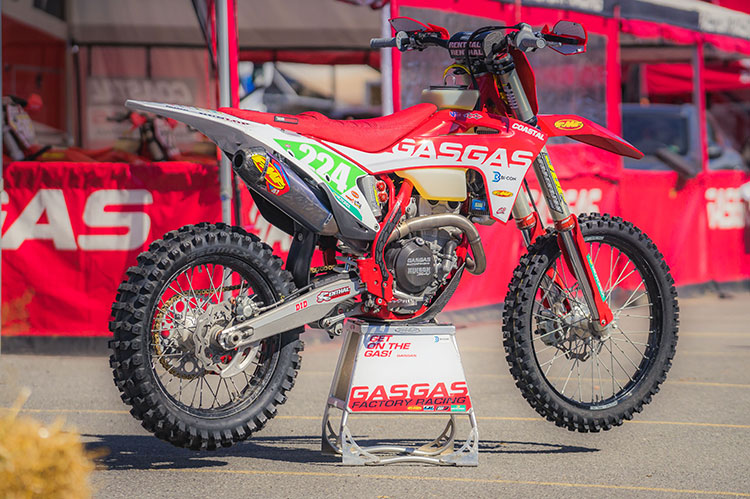
The likes of Ricky Russell and Johnny Girroir are some of the fastest on the east coast and deserve nothing less than factory bikes, which they have in the form of GasGas EX models. The difference between the MC and EX models is very minimal, but their base is an EX350F for Ricky and an EX250F for Ricky. So what goes into a Factory GasGas off-road bike? Let’s take a deep dive and see what makes these machines so special.
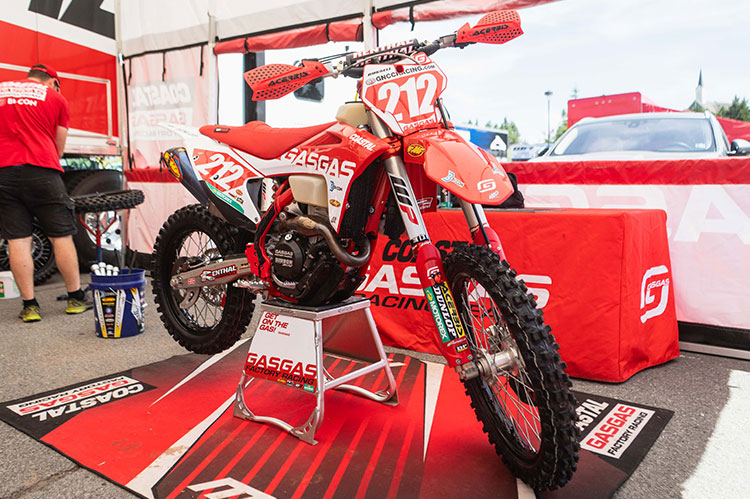
Starting with the motors, the two big dogs run Factory Services engines. GasGas headquarters handles everything engine wise and they have their off-road spec engines ready to go for these guys. Most of the factory and factory-supported teams are on this program and run similar to the same motor packages. For the amateurs, they run mostly stock engines with a little mapping to tailor it to the riders.
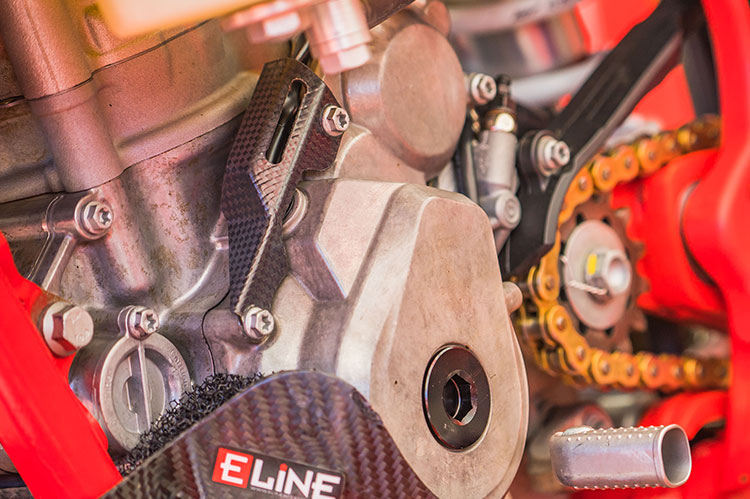
Hinson CLutches help with durability and a nice feel, and that’s very important when riding in the tight woods for 3+ hours every weekend. FMF supplies the exhausts for the team and IMS ensures they get the fuel they need.
Onto the chassis, the Coastal crew doesn’t have to do much. They equip all of their bikes with WP XACT Pro Forks and Shocks. This is a staple on every Austrian factory machine, and with the help of WP technicians that attend every race and spend countless hours testing and fine tuning settings with these guys, they usually work pretty good.

After talking with Barry Hawk, famed GNCC champion turned team manager of the Coastal Racing team, Ricky Russell is at one with his machine and is very particular about his setup. After racing on JDP Suspension settings last year (the same company who works with the amateur racers on Coastal), it admittedly took a while to grow accustomed to and find a WP factory setting that he liked, but Ricky eventually found it with help from Barry himself partaking in the testing process. Meanwhile, Johnny G is a rider who can ride seemingly anything fast and setup is less crucial.
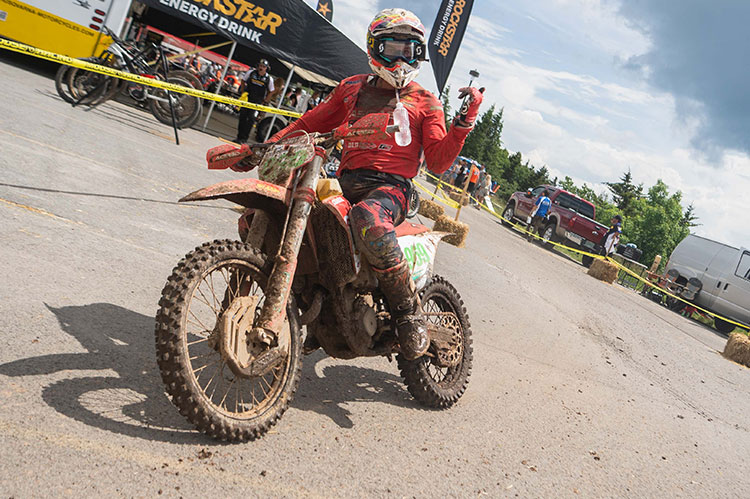
Additionally, they run the split triple clamps straight out of the PowerParts catalog, which we and many others say help with a supple feel and actually make the suspension feel softer than it is, in a good way. Seat Concepts is their seat cover sponsor, and almost every rider now runs a seat bump. They didn’t always run one until Ricky and Johnny did, then the riders transitioned over. In the mud, it really helps keep you in place on the seat and allows you to relax your arms a bit over the duration of the race. For footpegs, they all use IMS Core pegs with the exception of Ricky. He runs Fastway Ext footpegs with the extended ankle saver out back. Nihilo Concepts Billet Throttle Housing is in place for durability purposes as it is stronger than the cast aluminum unit.
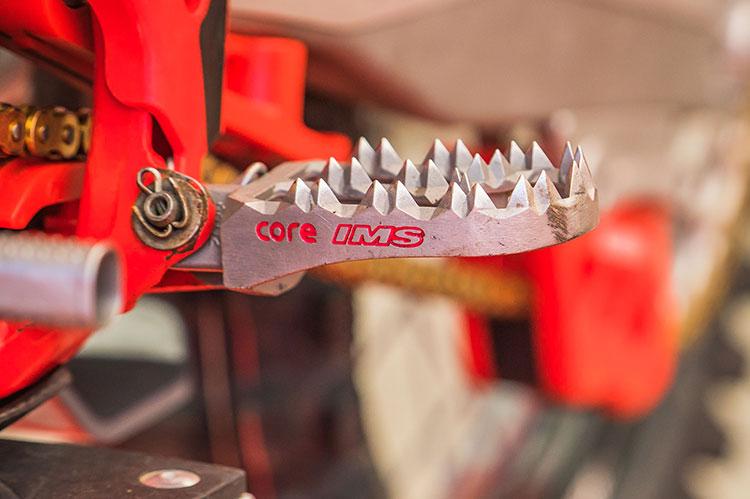
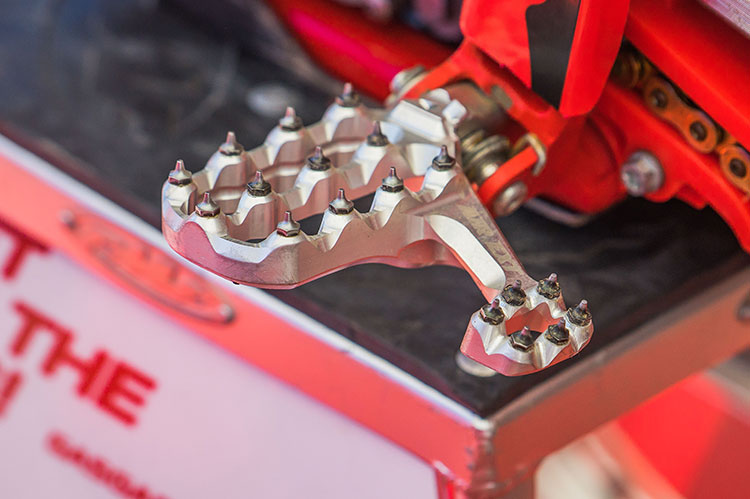
Renthal handles the handlebar/sprocket combo for the team. Interestingly, most of the guys, including Johnny, run 50T rear sprockets on the 250F’s, despite their conditions being much slower and tighter. On our KTM 250F with the same transmission ratios, we elected to go up from 51T to a 52T to close the gap and help keep the revs up. However, with first gear being pretty low on the bikes, dropping to a 50T can make it more usable in the tighter trees and rocks. For handlebars, rider preference determines the bar bend and whether they use a Fatbar or a Twinwall handlebar. DID Chains are always solid and the team relies on them for a durable setup.
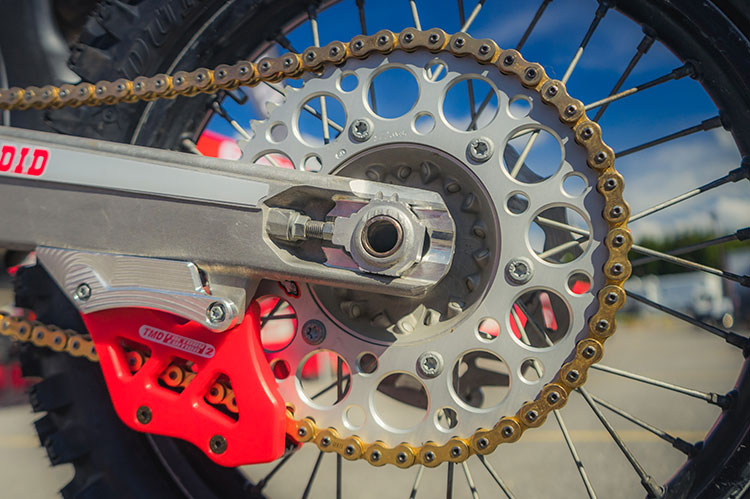
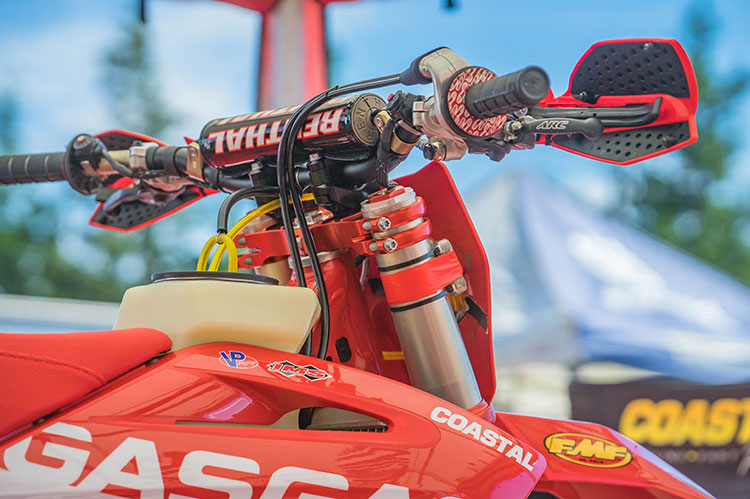
Dunlop is in charge of their tire needs and the common setup is either a MX3SF or MX33F front tire and an AT81 rear tire at almost every race. For Snowshoe, the team grooved the rear tires to help get a little more flex out of the knobs to better grip the slimy rocks and roots. In talking with Broc Glover of Dunlop, Stu Baylor is pioneering running different tire configurations back east. He regularly experiments with MX33 rear tires and MX53 tire combos depending on the terrain rather than sticking with just one tire combo. Thad Duvall and others are branching out slightly and taking a look at what other Dunlop tire combos they can run to suit the terrain better. Interestingly enough, I asked about running a gummy rear tire at Snowshoe which could be a huge advantage given the rocky and slimy terrain, but the Coastal guys didn’t think it’d last the duration. However, a Pro level rider did run a gummy rear tire and it held up very well, so expect to see some trying this out next year at Snowshoe.
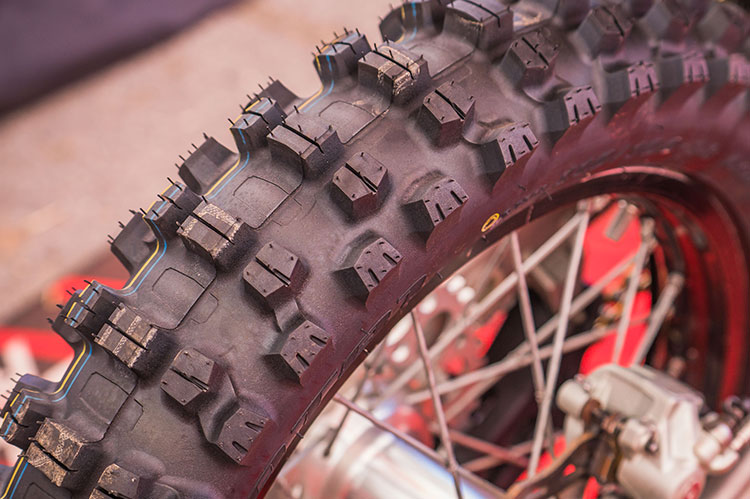
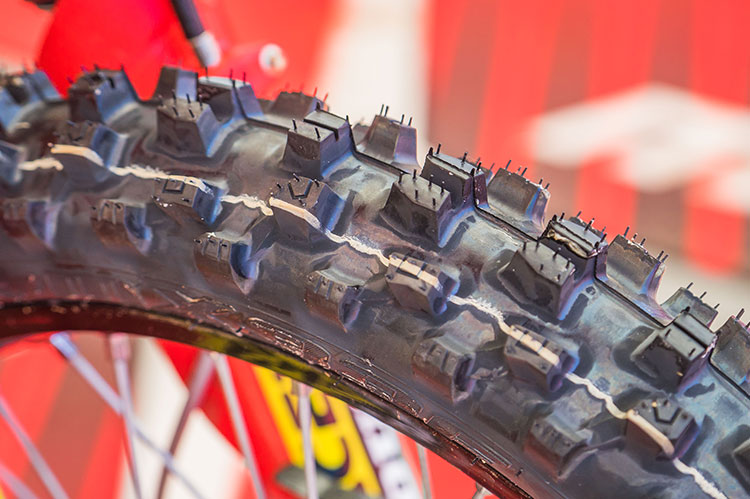
For protection pieces, they use the standard in terms of KTM’s proven setup. A PowerParts Skid Plate, TM Designworks Slide-N-Guide Kit, Bullet Proof Designs Swingarm Guard, ZipTy Shark Fin, and Acerbis Front Disc Guard are all in place. The amateur racers swap out the factory skid plate for an E-Line Carbon Skid Plate, but the rest is the same. Acerbis plastics and handguards are the final touch. Only one rider on the team, Shawn Remington in the 40+ A class, runs wraparound handgaurds. None of the younger riders do and most of the Pro riders on the circuit elect for flag style handguards.
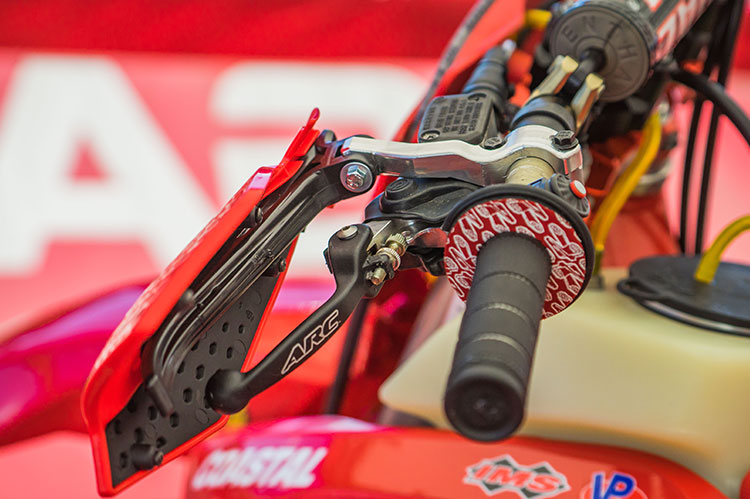
GNCC still starts the old school way with dead engine starts, and with every bike on the line being electric start, lighting up quick is essential for a good start. The team uses two 12V Super B batteries for a 24V system. With this, the bikes start much quicker and can be the difference between first and tenth off the line. The system seems to work too, as Ricky Russell is often at or near the front of the pack heading into turn two.
The two factory stars have Factory Brembo brakes at the controls while the amatuer crew uses the plenty good stock brakes with DP Brake Pads in place. Twin Air covers the air filters with filter skins and protects the radiators from mud with the mud sleeves. The bikes run on Motorex Oil and Evans Waterless Coolant.
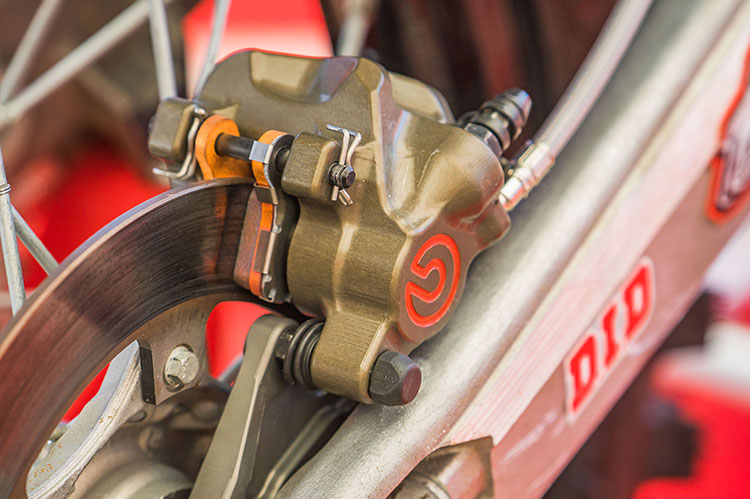
The real special part about a modern day factory bike is the team of technicians surrounding it and the attention to detail. With stock bikes being so good, there’s no need to go 1985 Honda RC250 level on them and ride something so far off from stock. The little pieces that add durability and protection all over the bike are pretty impressive and will have us looking to fine tune our own bikes for future races.